What Is the Impact of 4D Printing on Manufacturing?
First off, 4D printing is revolutionizing how manufacturers approach product design and production. Traditional manufacturing often requires separate components to be assembled later. With 4D printing, you can print objects that transform themselves into their final shapes or functions. Imagine a flat piece of material that, when heated, unfolds into a complex structure. This ability to create adaptable products not only simplifies the production process but also reduces the need for multiple parts and assembly lines.
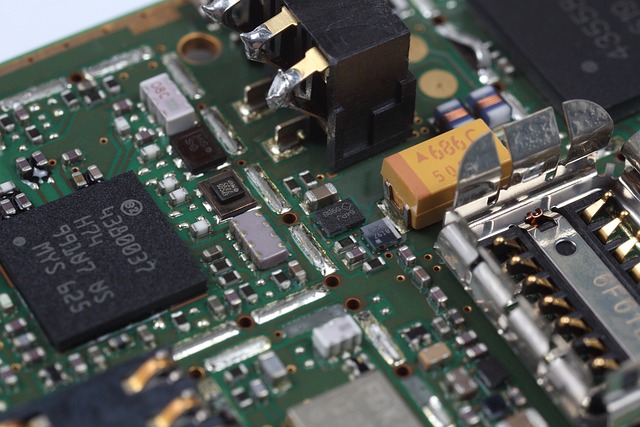
In addition, 4D printing could significantly cut costs in manufacturing. By minimizing waste and the need for manual assembly, manufacturers can achieve more streamlined operations. The ability to create complex shapes and functional parts in one go means fewer materials and less labor, which translates into savings.
So, while 4D printing is still evolving, its impact on manufacturing is already profound. It promises to transform how we design, produce, and utilize products, leading to more efficient, adaptive, and sustainable manufacturing practices.
Revolutionizing the Industry: How 4D Printing is Shaping the Future of Manufacturing
So, what exactly is 4D printing? While traditional 3D printing focuses on creating static objects layer by layer, 4D printing adds a thrilling twist: time. Picture this: objects made from smart materials that respond to environmental changes. When exposed to heat, moisture, or other stimuli, these objects can transform their shape or even perform different functions. It’s like magic, but it’s all science.
Think of it like this: If 3D printing is building a model airplane that stays the same forever, 4D printing is creating a plane that can unfold its wings or change its shape mid-flight based on how it’s being used. The potential applications are staggering. From self-assembling furniture that adjusts to your space needs to medical devices that morph to better fit the human body, the possibilities are endless.
What makes 4D printing so revolutionary is its ability to reduce waste and enhance functionality. Instead of manufacturing multiple components and assembling them, you can print a single piece that adapts as needed. This could significantly cut down on material waste and assembly time, making production more efficient and sustainable.
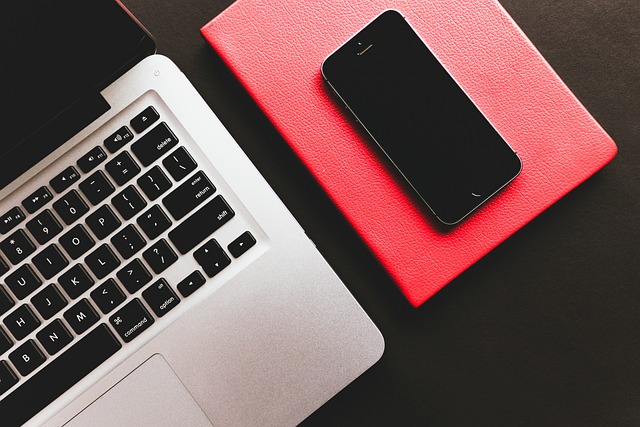
From Static to Dynamic: The Transformative Power of 4D Printing in Modern Manufacturing
How does this work? Picture a simple plastic sheet that, when exposed to heat or water, morphs into a complex, pre-designed structure. This isn’t magic—it’s 4D printing in action. By incorporating materials that react to external stimuli, manufacturers can create products that adapt to different conditions or requirements. For instance, imagine a self-repairing material that could automatically mend small cracks in a car’s bumper or a tent that expands and contracts based on weather changes.
This technology offers unparalleled flexibility and efficiency. Traditional manufacturing methods require separate processes for different functionalities, but 4D printing streamlines this by embedding adaptability directly into the product. Think of it as upgrading from a static, one-size-fits-all shirt to a wardrobe that adjusts to fit you perfectly based on your needs and activities.
Moreover, 4D printing can drastically reduce waste and improve sustainability. By designing objects that can change their purpose or form, fewer materials are needed, and products can be reused or repurposed rather than discarded. This not only saves resources but also reduces the environmental impact of manufacturing processes.
As industries begin to explore and adopt 4D printing, the possibilities seem limitless. From customizable consumer products to advanced medical devices that adapt in real time, 4D printing is poised to revolutionize how we approach manufacturing, offering a glimpse into a future where our creations are as adaptable as our needs.
4D Printing: The Next Frontier in Manufacturing Innovation and Efficiency
How does this magic happen? Well, 4D printing uses smart materials that respond to external stimuli like heat, moisture, or light. This means your printed object could shift shape or repair itself when conditions change. For instance, a 4D-printed chair might expand to become more comfortable as it warms up in the sun or a medical implant could reshape to better fit the body’s internal environment. The possibilities are nothing short of revolutionary.
But why should we care about 4D printing? First off, it could significantly streamline manufacturing processes. Imagine reducing the number of parts and assembly steps by having a product that self-assembles or adapts on its own. This efficiency not only saves time but also cuts down on waste. The adaptability of 4D-printed materials could mean fewer resources spent on creating multiple versions of a product.
Then there’s the potential for innovation in fields like aerospace, automotive, and healthcare. In aerospace, for example, parts could adjust to different flight conditions, improving performance and safety. In healthcare, implants that adjust to the body’s needs could lead to more personalized and effective treatments.
In essence, 4D printing isn’t just a new way to manufacture—it’s a game-changer, pushing the boundaries of what we thought was possible and opening doors to a future where technology and nature work hand in hand.
How 4D Printing is Redefining Manufacturing Processes and Product Design
4D printing takes traditional 3D printing a step further by introducing a time-based element. Unlike its predecessor, which creates static structures, 4D printing involves materials that can change their shape or properties in response to environmental stimuli. Think of it as a magic trick where your printed object isn’t just a one-off but something that evolves and adapts.
So, how does this work? Essentially, 4D printing uses special materials, often called smart materials, which can alter their form or function when exposed to specific triggers like heat, light, or moisture. Imagine printing a chair that can adjust its firmness based on how much weight it’s holding or a self-repairing drone that can mend its own cracks over time.
This dynamic ability opens up a whole new realm of possibilities in manufacturing. For instance, engineers can design parts that optimize their function only when they encounter certain conditions. This means less waste, more efficiency, and products that last longer and perform better.
In terms of product design, 4D printing allows designers to think beyond the constraints of static forms. They can create objects that transform, adapt, or even self-assemble, leading to innovative solutions in industries like aerospace, healthcare, and automotive. This could mean safer, more customizable medical implants or vehicles that adjust their aerodynamics based on driving conditions.