How Are Digital Twins Revolutionizing Industry?
In industries like aerospace or automotive, digital twins are crucial. They simulate how an aircraft engine or a car performs under different conditions, providing insights that drive innovations and improvements. It’s like having a crystal ball for predicting performance, but instead of mysticism, it’s grounded in data and simulations.
Digital twins are also revolutionizing construction and real estate. Imagine building a skyscraper; with a digital twin, you can visualize every stage of the construction, anticipate potential issues, and streamline the process. It’s like having a detailed blueprint that evolves and adapts in real time, making project management a lot smoother.
But the magic doesn’t stop there. Cities are using digital twins to optimize traffic flow, reduce energy consumption, and improve public services. By creating a virtual version of an entire urban area, planners can test different scenarios and make data-driven decisions that enhance the quality of life for residents.
In essence, digital twins are the ultimate fusion of the physical and digital worlds. They allow industries to innovate, optimize, and predict with unprecedented precision. If you haven’t yet embraced this technology, it’s high time you start imagining how your industry could be transformed.
Digital Twins: The Game-Changer Transforming Modern Industry
A digital twin is like a high-tech doppelgänger of a physical entity. It’s a dynamic digital model that mirrors every nuance of its real-world counterpart. This concept is more than just a futuristic idea; it’s a game-changer that’s already making waves across various sectors.
Think of it like this: If you’re managing a factory, a digital twin of the production line lets you simulate changes, spot inefficiencies, and predict failures without ever shutting down the actual line. It’s like having a crystal ball that reveals how tweaks will impact performance before you even make them. No more guesswork or trial-and-error—just data-driven decisions that save time and money.
But it’s not just about efficiency. Digital twins are transforming industries by enabling smarter design and maintenance. For instance, in the realm of construction, architects and engineers use digital twins to visualize building projects, foresee potential issues, and ensure everything fits perfectly before the first brick is laid. It’s akin to having a detailed map before setting out on a journey; it guides you around obstacles and charts the best course.
Healthcare is also reaping the benefits. By creating digital twins of patients, doctors can simulate different treatments and predict outcomes with unprecedented accuracy. Imagine having a personalized medical blueprint that helps doctors tailor treatments specifically to your needs.
In essence, digital twins are the unsung heroes driving the next wave of innovation. They’re making industries smarter, more efficient, and remarkably responsive.
How Digital Twins Are Redefining Operational Efficiency Across Sectors
Digital twins create a dynamic, virtual model of physical assets. Think of it as having a digital clone that’s always in sync with its real-world counterpart. This means you can monitor, analyze, and even predict issues before they become costly problems. For instance, in manufacturing, a digital twin of a production line can simulate different scenarios, optimizing performance without any real-world trial and error. It’s like playing a video game where you can test strategies and see the outcomes before making any actual moves.
In sectors like transportation and logistics, digital twins can revolutionize operations by mapping out entire fleets of vehicles. By using these digital models, companies can foresee maintenance needs, avoid downtime, and improve route planning. It’s akin to having a GPS that not only guides you but also warns you about potential roadblocks ahead.
Healthcare is another arena where digital twins are making waves. Imagine virtual replicas of medical equipment or even patient health profiles, helping doctors predict complications and personalize treatment plans. This proactive approach is like having a doctor who knows what’s coming next, making each intervention more precise.
Digital twins are more than just a buzzword; they’re the cutting-edge tool driving unprecedented levels of operational efficiency. By providing real-time insights and predictive analytics, they help businesses fine-tune their operations, cut costs, and stay ahead of the curve.
The Rise of Digital Twins: A New Era of Innovation in Manufacturing
Picture this: You have a factory with machines running day in and day out. Instead of waiting for something to break down or underperform, a digital twin of each machine allows you to monitor its condition in real-time. It’s like having a supercharged crystal ball that tells you exactly how each machine is performing, and even predicts potential failures before they happen. This isn’t science fiction—it’s the new reality in manufacturing.
The rise of digital twins has created a massive shift in innovation. These digital replicas allow manufacturers to simulate production processes, test new designs, and tweak operations without physically touching a single piece of machinery. Imagine running countless virtual experiments to find the perfect design or operation tweak—all without the hassle of real-world trial and error. It’s efficiency on steroids!
Moreover, digital twins help in optimizing the entire lifecycle of a product. From design to end-of-life, these digital counterparts provide insights that were previously unattainable. They enable better decision-making by offering a detailed understanding of how products perform in various conditions. It’s like having a GPS system for every product’s journey through its lifecycle.
In essence, digital twins are ushering in a new era of manufacturing—one where innovation, efficiency, and predictive maintenance become the norm. This cutting-edge technology is setting the stage for a smarter, more agile industry, transforming the way we think about manufacturing.
From Simulation to Reality: The Impact of Digital Twins on Industrial Processes
Think of a digital twin as a high-tech mirror reflecting your physical assets. By simulating real-world processes in a digital environment, you can test changes and predict outcomes without risking actual downtime. This isn’t just theory; it’s practical and actionable. For instance, if you’re thinking about upgrading a production line, you can model this change virtually. The digital twin will show you how it impacts everything from output to energy consumption before you make the investment.
Why is this so groundbreaking? Imagine diagnosing and fixing a problem before it even happens. Digital twins provide a playground for troubleshooting, allowing you to run “what-if” scenarios. Need to know how a new machine will affect your workflow? Run the simulation, tweak the parameters, and get the answers you need. This proactive approach helps prevent costly disruptions and streamlines maintenance.
But it doesn’t stop there. Digital twins also enable continuous improvement. By analyzing real-time data from the physical plant, they offer insights into inefficiencies and bottlenecks that you might not catch otherwise. It’s like having a crystal ball that shows you exactly where your processes could be fine-tuned for optimal performance.
In essence, digital twins are the bridge between theory and practice, allowing industries to innovate and improve with precision. They bring a new level of clarity and control to complex industrial processes, making it easier to stay ahead of the curve and maintain a competitive edge.
Unlocking the Future: How Digital Twins Are Shaping the Industrial Landscape
So, how does this magical digital mirror work? Picture it like having a twin who lives in the digital world. This twin mimics every move, every change, and every glitch of its real-world counterpart. By tapping into real-time data, it can simulate scenarios, predict outcomes, and even suggest improvements before anything goes wrong. It’s like having a crystal ball that’s constantly updating itself with the latest insights.
Now, consider the impact on industries. Imagine an automotive plant that uses a digital twin to test out new assembly processes without actually touching a single car. Or think about a power plant that can forecast maintenance needs, preventing downtime before it even starts. The potential is enormous. Digital twins allow businesses to make smarter decisions, optimize operations, and save money—all while keeping risks at bay.
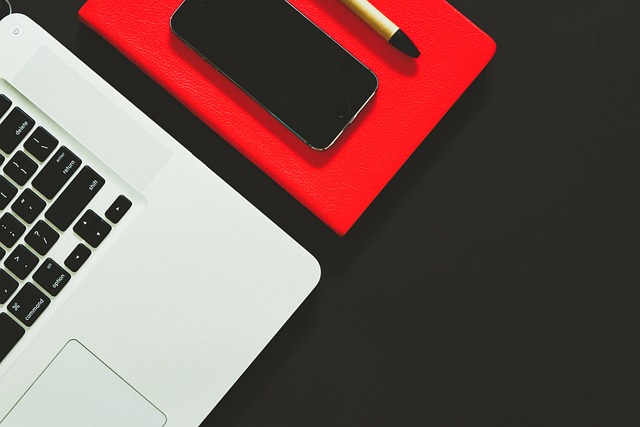
In essence, digital twins are the unsung heroes of the modern industrial era. They offer a blend of foresight and flexibility that was once the stuff of science fiction. If you’re looking to stay ahead in a competitive market, embracing this technology might just be your golden ticket.
Revolutionizing Maintenance: The Role of Digital Twins in Predictive Analytics
Think of a digital twin as a high-tech crystal ball that gives you a detailed look at how your equipment will perform in the future. By simulating various conditions and scenarios, it can pinpoint potential failures and inefficiencies long before they become critical. It’s like having a personal mechanic who knows your equipment inside and out, but operates in the digital realm.
This technology works by collecting data from sensors embedded in physical assets. This data is then used to create a virtual model that mirrors the physical asset’s condition and performance. With this model, you can test different maintenance strategies and see their effects without any risk. This means fewer costly downtimes and more streamlined operations.
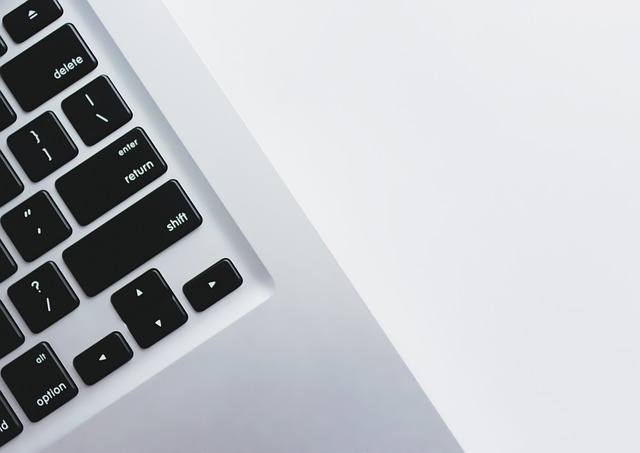
So, if you’re tired of unexpected breakdowns and hefty repair bills, digital twins could be the game-changer you need. They transform reactive maintenance into proactive management, giving you the ultimate tool to keep your systems running smoothly and efficiently.